Value Engineering, VIPs, Lean
Value Engineering (VE) can be a tremendously effective process. As part of our portfolio of services, we use this process for clients around the globe to derive a number of benefits (optimization of cost, scheduling and functionality) for a wide range of topics. It is important to know that there are various conflicting interpretations regarding the VE process: i.e. its process steps, required resourcing, its deliverables and potential outcomes.
VE started in the manufacturing industry as Value Analysis in the General Electric Company of the United States in the 1940s. Since then it has been used in private industry and by government agencies as a method for cost reduction, improved product/project development and product/project improvement/re-engineering. It is also used as a tool for business process improvement.
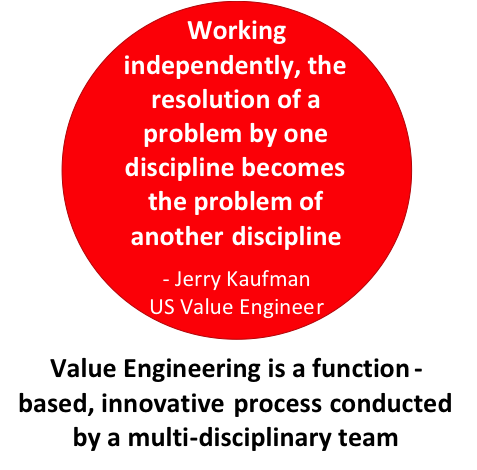
Value takes into account the total cost of ownership as well as compliance with users' requirements, reliability of performance, appropriate quality and functionality, along with after-sale support where applicable. Value can vary between different stakeholder opinions and can change with circumstances and over time.
Lawrence Miles, working in procurement in GE, is known as the “father of Value Engineering”. He stated that:
“All cost is for function” (Use, esteem/aesthetics or exchange function)
“Thinking by function allows greater freedom for creativity”
Analysis by function is a critical step in effective Value Engineering.
In the United States, Value Engineering is specified in Public Law 104-106 (February 1996), which states “Each executive agency shall establish and maintain cost-effective Value Engineering procedures and processes. DEFINITION.- As used in this section, the term 'value engineering' means an analysis of the functions of a program, project. system, product, item of equipment, building, facility. service or supply of an executive agency, performed by qualified agency or contractor personnel. directed at improving performance, reliability, quality, safety and life cycle costs."
With over a quarter of a century of conducting highly successful VE assignments, as well as certification training, we know that there are no shortcuts to effective VE. The focus and emphasis of the VE process can, with expert guidance, be adjusted to suit the circumstances of application. A “one-size fits all”, minimalist approach is to be discouraged. That said, we are proud of the outstanding results that we have guided within very short timeframes.
Value Engineering (VE) is an intensive, interdisciplinary problem-solving activity that focuses on improving the value of the functions that are required to accomplish the goal, or objective of any product, process, service, or organization.
Value Engineering is conducted through the use of the Value Methodology.
Value Methodology: “The systematic application of recognized techniques which identify the functions of the product or service, establish the worth of those functions, and provide the necessary functions to meet the required performance at the lowest overall cost.” John M. Bryant, VM Standard, Society of American Value Engineers, Oct. 1998.
The cost-benefit of conducting effective VE is tremendous. However, attempts to reduce the number of VE phases would be counter-productive cause a disproportionate loss of effectiveness. As well, overloading the VE process with non-required participants will also reduce efficiency of interactions and outputs.
The addition of risk evaluation at the beginning and end of the traditional VE phases improves the practicality of outcomes of traditional VE. Similarly, the formal use of performance metrics and related analyses vastly aids the smooth application of the VE process and corresponding results.
The terms value analysis and value management are often used as being synonymous with VE; on the other hand, some jurisdiction interpret them differently. The VE process and examples of application are described in our Knowledge Bank.
Combining the value and risk management (VRM) approaches is a particularly powerful method, especially when integrated within the traditional project development process.
Download “A Value and Risk Management Approach to Project Development” paper, as published in the Proceedings of the Institution of Civil Engineers.
🔷🔷🔷
A Note on VIPs
Overview
Typically, Value Improving Practices (VIPs) are applied within an organization's formal, gated project management process. There can be some overlapping of individually applied VIPs. VIPs are not “business-as-usual”; by definition, VIPs must not be routine. Typically, VIPs are out-of-the ordinary practices used to improve cost, schedule, and / or reliability of large capital construction projects. VIPs are applied early in the project, at the definition or Front End Loading (FEL) stage. Only practices with a demonstrated, statistically reliable correlation between use and better outcomes are deemed VIPs.”
The number and definition of VIPs can vary between organizations.
Example application areas are: oil and gas, petrochemicals, manufacturing and pharmaceuticals.
It will be seen that there are many related applications and there can be some overlapping of individually applied VIPs. Other VIPs, such as constructability and value engineering are applied more than once, as needs dictate. In practice, the traditional value methodology is an analytical and creative consensus building process that guides the application and achieves many of the stated objectives of the other VIPs.
Some large industrial projects are recognizing and enforcing the application of a sequence of stage gates and their own list of preferred VIPs. A VIP must provide an improved project outcome. Further, a VIP must not improve one outcome at the expense of another. Newcomers to project management may well be confused by the vast array of terminology and apparently similar techniques. It is not surprising, therefore, that many people prefer to remain with a minimal number of familiar techniques and resist taking on any new ones. Caution must be exercised to not use the VIP process as a check box system in order to just give the impression that best value is being attained.
List of VIPs
Several of the intended VIPs’ objectives can be achieved quickly and effectively through an integrated and selective application of the value methodology.
The following text outlines several VIPs. The list is neither exhaustive nor universally agreed. Many of the VIP descriptions indicate outcomes, rather than processes. These outcomes are natural products of a comprehensive value enhancement process. It could be argued that some are just special practices unique to a particular circumstance.
A. Class of Facility Quality
Definition of the best value facility classifications to meet the Business Plan requirements in terms of specific aspects.
B. Technology Selection
Identification and evaluation of the technology most appropriate to meet the defined business need.
C. Process Simplification
Reduction of unnecessary investment and operating processing costs.
D. Design to Capacity
Avoidance of over-sizing components and systems to meet the defined business need.
E. Waste Minimization
Reduction of waste at source and re-use of waste for cost-effectiveness.
F. Customized Standards / Specifications / Practices
Customizing of standards, specifications and practices that are appropriate to the application and not excessive to the defined needs of the specific facility.
G. Energy Optimization
Maximization of total return on investment by judicious selection and use of plant utilities and equipment.
H. Facility Optimization
Reduction in overall return in investment and operating costs by combining or making unnecessary one or more chemical or physical processing steps.
I. Constructability
Analysis of a design by experienced construction personnel to reduce costs and save time during construction.
J. Value Engineering
Identification of alternatives for meeting functionality and quality requirements at the least life cycle cost.
K. Predictive Maintenance
An approach to maintaining a facility whereby equipment is monitored and repairs are made before failure, thus increasing uptime, product quality and yield, as well as stretching effectiveness of capital investment.
L. Life Cycle Impact Assessment
In conjunction with external stakeholders, a triple bottom line (social, environmental and financial) approach to determining most appropriate solution for the total life cycle.
M. Systems Optimization
Efficiency reviews to optimize an in-service process or facility.
N. Reliability Improvement
Provides an effective way to cost justify maintenance activities, decrease equipment downtime and identify solutions with a high return.
O. Risk Assessment and Management
Risk-based decision making and management of risks.
P. Supply Chain Optimization
Integration of the entire supply chain (e.g. suppliers and installers) for full potential in terms of optimizing cost, schedule and quality.
Q. Partnering
Trust based process that focuses owner and service provider(s) on creative cooperation and avoidance of confrontation for mutual financial benefit.
R. Performance Criteria & Measures
Project Performance Criteria and Measures are used to provide stakeholders with an opportunity to explicitly model project performance, especially in terms of scope, functionality, schedule and budget.
S. Design to Cost
Controls cost throughout the design process by defining not-to-exceed cost targets for each system and subsystem of the project or product.
Application of VIPs
With such an array of individual VIPs to choose from, a project specific VIPs scoping review should be undertaken and a VIP plan defined.
This should include which VIPs will be used, timing of application, key team members and the required outcomes. It is better in practice if there is consistency of VIP team, value methodology and risk management core team members. VIPs and their objectives are generally best accomplished not by addressing each one separately, but by judicious selection, combination and timing of application.
Value engineering is an effective process for achieving the defined deliverables of the other Value Improvement Practices. Most VIPs are, in practice, the objectives or focus of the application of the value methodology. A typical Value Study will encompass the objectives of several VIPs.
Incorporating Lessons Learned
Lessons learned are incorporated, as appropriate, from other projects. Capturing of lessons learned can follow the process steps of: Identify lesson/practice; Document; Validate; Communicate; Extract; Transfer; Apply.
This should be done on a progressive basis rather than waiting for the final close-out and the close-out report.
Each VIP Champion should be made responsible for the lessons learned process in his/her area.
🔷🔷🔷🔷🔷🔷

Lean Business Process/Approach
The key principles of Lean Six Sigma Business Transformation are:
1. Focus on the customer
2. Identify and understand how the work gets done (the value stream)
3. Manage, improve and smooth the process flow
4. Remove Non-Value-Added steps and waste
5. Manage by fact and reduce variation
6. Involve and equip the people in the process
7. Undertake improvement activity in a systematic way.
Example Application: Elimination of Waste in Health care System
Lean helps generate savings by decreasing waste, decreasing medical errors and refining quality. It can also help in improving patient report conclusions and recognizing, preventing, and managing prolonged disease.
The three types of waste in health care—administrative, operational, and clinical. Both administrative and operational waste are constituents of inefficient production. Clinical waste is a type of allocative waste.
• Administrative waste is the excess administrative overhead.
• Operational waste denotes to other aspects of inefficient production processes.
• Clinical waste is waste created by the production of low-value outcomes.
Lean Six Sigma Approach to Managing Projects (DMEDI)
The five phases for managing projects include:
• Define the project purpose, establish goals, structure and identify the value for the customer and company
• Measure throughout the process and project completion by determining how you will quantify success
• Explore new ways to accomplish completion of the project to continually improve the process
• Develop a comprehensive plan, including personnel and financial resource needs, to organize and implement the project as identified in the define phase
• Implement the project plan for completion
A variety of management tools and techniques are used within the DMEDI overall guiding framework and continuous improvement approach.
🔷🔷🔷
There are many views of what constitutes Lean and related processes. These views vary from a lengthy, statistics based, efficiency improvement process to a method for quickly identifying and eliminating unnecessary features/actions to reduce the “bottom line”. Various descriptions and opinions abound. A number of bodies offer advice on Lean and related method.
Lean enables organizations to optimize across the value stream for value delivery, improving speed, quality, and organizational health. The Lean method is a philosophy centered around eliminating waste and providing the best customer experience. According to the Lean method, there are eight kinds of waste that can occur at the work site and in the office:
- Defects
- Overproduction
- Waiting
- Non-Utilized Talent
- Transportation
- Inventory
- Motion
- Extra Processing.
Linking Lean and Six Sigma
Six Sigma is a data-driven problem-solving methodology. The focus is on process variations and emphasis is given to customer satisfaction. The goal of Six Sigma is to make a process effective with - 99.99996 % defect free. This means a six sigma process produces in 3.4 defects per million opportunities or less as a result. Problem-solving in Six Sigma is conducted using the DMAIC framework. There are five stages in this framework. DMAIC is the more well-known and most-used Lean Six Sigma project methodology and is focused on improving an existing process,
D Define the problem with the product or process.
M Measure the current process and collect data.
A Analyze the data to find the root causes of defects.
I Improve the process based upon the data analysis and test it.
C Control new process and monitor for defects.
For creating a new product or process, the DMADV steps are used:
D Define process and design goals
M Measure critical-to-quality aspects of the proposed new process/product, including risks and production capabilities
A Analyze to develop process designs and evaluate to select the best design for the new process
D Design process details and optimize your design. Test your design(s)
V Verify the chosen design for your process with pilot-testing. Implement and monitor the new process
Lean Production
Lean manufacturers arrange production in closely located ‘cells’ so that work flows continuously, with each step adding more value to the product. The standard time for all activities is known and the objective is to totally eliminate all stoppages in the entire production process. However, only optimum stocks of material are kept as buffers between processing stages.
For this system to be effective, every machine and worker must be completely capable of producing repeatable perfect quality output at the exact time required. Workers are responsible for checking quality as the product is assembled, and in some instances given authority to stop production if defects arise. In this way, quality problems are exposed and rectified as soon as they occur.
The workforce is kept informed of progress towards their production and cost targets by use of information displays so that everyone is able to see the status of all operations at all times. Work teams in lean manufacturing are highly trained and multi-skilled, and many of the traditional supervisory and managerial functions have been devolved to them.
Lean manufacturing is based on the elimination of waste, including time lost waiting for missed/delayed supplies, unnecessary storage and the value tied-up in large stocks of parts waiting for assembly. ‘Just in time’ (JIT) delivery is therefore a vital element, and to deliver this lean manufacturers have had to develop their network of suppliers. Significant efforts are applied to encourage them to adopt the same lean manufacturing principles and systems, often company-wide, rather than solely related to that part of the suppliers’ operations that affect the manufacturer.
Lean manufacturers are moving away from traditional relationships with their suppliers to partnering arrangements with a smaller number based on good communications and open-book accounting. These relationships work by both parties sharing philosophies of continuous improvement (especially in the area of defect reduction, cost and timeliness of delivery) and sharing business and development strategies sufficient for both parties to know enough about each other to make forward planning effective.
Lean Construction
The Lean principles are applied in construction by focusing on improving the whole process. This means all parties have to be committed, involved, and work to overcome obstacles that may arise from traditional contractual arrangements.
Design
• Use of visualisation techniques such as Virtual Reality and 3D CAD to fully define the product requirements from the customer’s perspective.
• Value Management to achieve more understanding and focus on client value.
• Use of integrated design and build arrangements (including partnering) to encourage close cooperation between designers, constructors and specialist suppliers.
• Design for Standardisation and Pre-assembly - both of components and processes to achieve higher quality and cost and time savings.
Procurement
• Supply chain management and rationalisation of the supply chain to integrate all parties who contribute to the overall customer value into a seamless integrated process.
• Transparency of costs - the elimination of waste in both processes and activities requires a clear and complete understanding of costs to ensure decisions on customer value can be taken. Confidentiality of cost and cash flows must be addressed.
• The concept of partnering, all involved parties contributing to a common goal with the boundaries between companies becoming less critical.
Production Planning
• Benchmarking to establish ‘best in class’ production methods and outputs
• Establishment of a stable project programme, with clear identification of critical path.
• Risk management - to manage risks throughout the project
Logistics
• Just-in-time delivery of materials to the point of use eliminates the need for on-site storage and double handling
Construction
• Clear communication of project plans
• Training, teamwork, multi-skilling
• Daily progress reporting and improvement meetings
• A well motivated, well trained, flexible and fully engaged workforce.